聯電南科廠成為全球燈塔工廠!如何以「智慧製造」刷新半導體標準?
記者 鄧天心/綜合報導
聯華電子(UMC)位於台南科學園區的Fab 12A廠,近日被世界經濟論壇(WEF)納入「全球燈塔工廠網絡」(Global Lighthouse Network),成為全球首座獲此認證的半導體晶圓代工廠。
全球燈塔工廠網絡由世界經濟論壇與麥肯錫公司於2018年共同發起,旨在表彰成功運用第四次工業革命技術(如人工智慧、工業物聯網、大數據等)提升效能與獲利的指標性工廠,截至目前,全球已有189座工廠入選,涵蓋30個國家和35個不同產業。
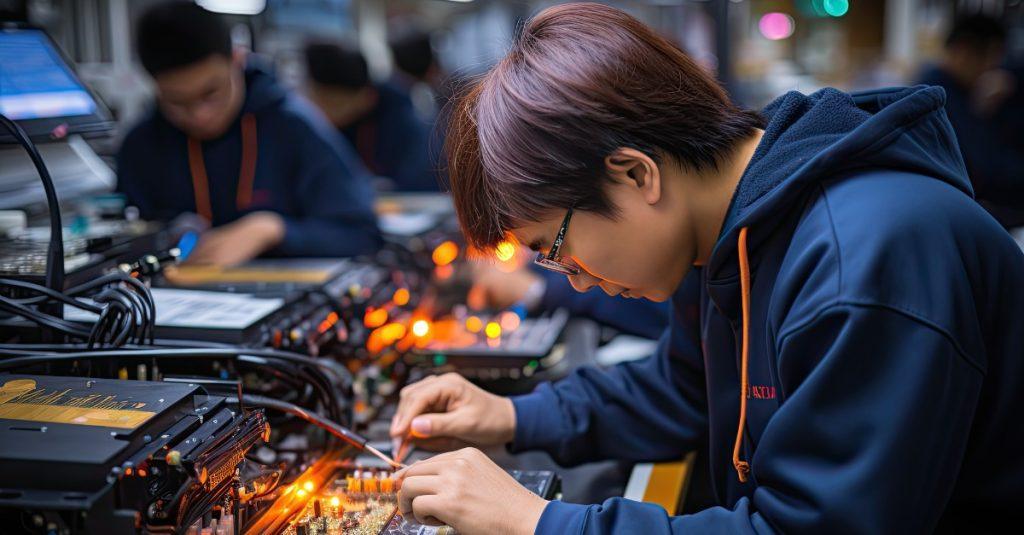
要獲得燈塔工廠認證,其中審核標準需要在生產過程中成功運用第四次工業革命技術(例如人工智慧、物聯網、大數據分析等),大幅提升效率和創造價值,聯電的Fab 12A廠導入了智慧缺陷真因辨識系統,這是一套結合人工智慧和影像識別的工具,用於快速找出製程異常的根本原因;這樣的技術使產品良率提升到97%,此外,廠區還使用了智慧氣體切換系統,減少了生產過程中機台調整的等待時間,顯著縮短了生產週期。
聯電也因為在節能減碳方面的努力也獲得肯定,以南科廠的冰水系統為例,聯電透過安裝感測器和AIoT(人工智慧物聯網)技術,優化能源使用,每年節省超過1,200萬度電,另外,聯電在成熟製程(例如28奈米和14奈米)上的技術不但穩定了成熟製程市場的供應鏈,也進一步吸引國際訂單。
更多新聞:凌華攜銳能推「EMS能源管理系統」電動車社區高效充電服務
從成立「智慧製造處」開始 開啟轉型之路
大家可能很好奇,為什麼聯電做了哪些努力可以獲得燈塔工廠的認證?其實早在2017年,他們就成立了一個專門負責數位轉型的部門,稱為「智慧製造處」,這個部門的任務是透過導入新技術來改進生產過程,並首先以南科的Fab 12A廠作為測試和示範基地,智慧製造處至今開發出超過48種解決方案,這些方案用於解決生產過程中的各類問題,例如提升效率、縮短交付時間,並優化產品品質。
聯電透過不斷優化,已經達到設計套件交付時程縮短了57%,代表新產品的開發和上市時間大幅縮短,他們的產品良率也提升至97%,表示每批晶圓中的合格產品比例非常高,減少了損耗,另外工作效率提高了47%,表明員工或機台的生產力得到了明顯改善。
聯電也在製造過程中導入機器學習模型預測、智慧氣體切換系統以及智慧缺陷真因辨識系統,以機器學習模型預測為例,聯電利用AI預測機台可能出現的問題,提前進行調整,減少停機時間;另外在智慧氣體切換系統方面則是因為在半導體製造中,但傳統上需要花費較多時間進行調整,聯電則是透過自動化的氣體切換系統,縮短了這部分的等待時間,讓整體生產週期加快;而智慧缺陷真因辨識系統則是結合了影像識別和AI比對技術,能夠迅速分析生產中的異常狀況,幫助工程師快速找出問題的根本原因,也有效地提升了產品的良率,降低了廢品率。
聯電在節能減碳方面也取得了顯著成果,以南科廠為例,針對耗能最大的冰水系統,透過加裝各式感測器及AIoT無線智能電錶,積極發展智能化及優化節能控制系統,在不影響產能的情況下,成功地節省了大量能源,讓節能效益提升了3%,年省電力達1,223.2萬度,節省能源成本達2,965萬元。
世界經濟論壇的認可不僅是對聯電技術的肯定,更代表了數位化浪潮對製造業的深遠影響。這激勵更多傳統產業進行創新轉型,也讓我們看到智慧製造和環境永續並非對立,反而可以相輔相成,這對其他資源密集型產業來說,這些都是非常具啟發性的案例。
瀏覽 1,824 次